There is a major dilemma surrounding drilling and fracking for oil and gas. On one hand, humankind can hardly survive without this source of energy. Our survival hinges on it. But on the other hand, the oil drilling and fracking processes have many adverse effects on the environment. All sorts of drilling chemicals are injected into the ground to boost the production of oil, degrading the environment around the drilling site. And this has got environmental activists going on and on about these detrimental effects.
There is a major dilemma surrounding drilling and fracking for oil and gas. On one hand, humankind can hardly survive without this source of energy. Our survival hinges on it. But on the other hand, the oil drilling and fracking processes have many adverse effects on the environment. All sorts of drilling chemicals are injected into the ground to boost the production of oil, degrading the environment around the drilling site. And this has got environmental activists going on and on about these detrimental effects.
Amongst these oil drill-optimizing chemicals are drilling fluids and additives. In this article, you’ll see:
- What drilling fluids and additives are, and why we use them in the oilfield.
- The different types of drilling fluids and additives.
- What you need to know about shipping these oilfield chemicals, including the challenges that befall them.
- And how Total Connection oilfield chemical logistics company is a solution to these challenges.
Drilling Fluids and Additives: What They Are Why We Use Them
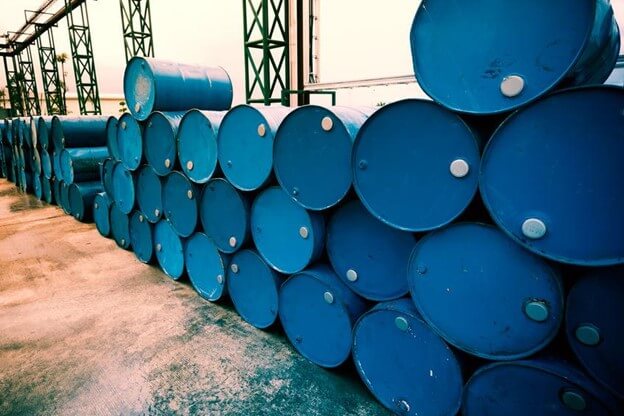
Drilling fluids, or drilling muds, are oilfield chemicals that help to ease the drilling of wellbores deep into the ground. And as the name suggests, operators add drilling fluid additives to drilling muds to help to boost the effectiveness of the drilling fluids. The combination of drilling fluids and additives makes the oil drilling process more efficient, while mitigating the environmental impacts and ultimately saving costs.
The needs of each oilfield are unique, depending on location, size of the operation, how challenging the job is, and many other factors. As a result, the fluid and additives used in oil production are numerous to help cater to these various needs in the oilfield.
The Different Types of Drilling Fluids and Additives
There is a long list of drilling fluids and additives types, with each serving a unique purpose in the highly complex drilling process. The following are the different types of drilling fluids and additives we use in oilfields.
Fluid Loss Control Agents
When drilling fluids are injected into wellbores to force oil out of fractures, the turbulence down there could lead to the loss of fluids. This is bad because uncontrolled fluid loss bears grave consequences on the environment. As a result, it is important to use fluid loss control agents to control the escape of drilling fluids into places they shouldn’t get to.
Defoamers
Some unwanted gases try to escape to the surface during the oil drilling process. These gases could drop the effectiveness of drilling fluids by a huge margin when they mix with the fluids. The muds then begin to foam to show that a lot of gases have been trapped within. That is why there is the need for defoamers. Defoamers are mud additives used to release the trapped gases in the drilling mud to send unwanted gas up to the surface.
Drilling Fluid Additives
Not only is oil drilling complex, but it’s also delicate. Too much alkalinity or acidity could ruin the entire process. That’s what oil producers invest in drilling fluid additives which help to adjust and regulate the pH levels of the drilling fluids. These chemicals keep the acidity and alkalinity of the drilling muds under control.
Alkalinity Control
Alkalinity control chemicals are similar to drilling fluid additives. They also help to regulate the pH level of the drilling muds. Examples of alkalinity control chemicals include citric acid, soda ash, lime, lime O, magnesium oxide, sodium bicarbonate, potassium hydroxide, caustic soda, and more.
Emulsifiers and Wetting Agents
Injecting drilling fluids at high rates could cause a lot of instability in the wellbores if there aren’t some chemicals in the drilling fluids. Examples of such chemicals are emulsifiers and wetting agents. Emulsifiers and wetting agents help reduce the surface tension in drilling fluids to improve their penetrating and spreading properties.
Pipe-Freeing Agents
Friction in pipes is also another problem that might have caused a lot of problems for oil drilling companies if there weren’t pipe-freeing agents. The drilling fluid could stick to some parts of the pipe and reduce fluid flow until it completely blocks the pipe. This is especially common in pipes that are angled in deviated wellbores. To combat the situation, oil companies use pipe-freeing agents. Examples of pipe freeing agents include soaps, glass beads, oils, surfactants, soda lime, cationic polyacrylamide, and many more.
Lubricants
It’s no news that friction could be a major oil drilling problem if untended. Fortunately, there are many oilfield chemicals that help to combat it. An example of such chemicals are lubricants. Lubricants help to reduce drag and torque in the drill bit, thereby putting all the generated horsepower to effective work. Examples of lubricants include diesel oil, different kinds of vegetable oils, fatty acid esters, graphite powder, asphalt blends, soaps, air-blown asphalt colloids, and many more.
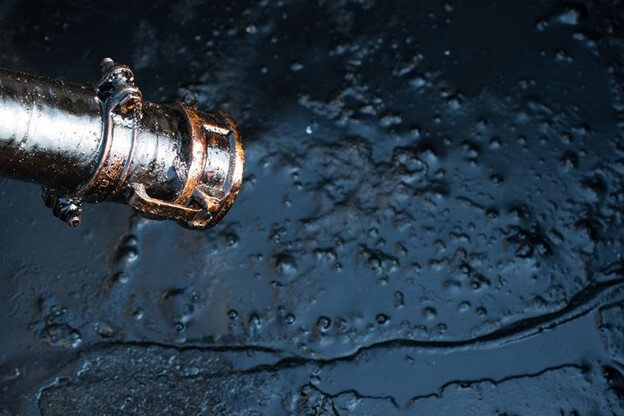
Temperature Stabilizers
Oilfields in high-temperature regions always need to maintain thermal stability. There is also the need to boost the stability of the filtration and rheological properties of the drilling fluids. We use temperature stabilizers in oilfields for these two main reasons.
Viscosifiers
There are some drilling situations where high viscosity drilling fluids are needed. And this often happens when there are rock cuttings to float to the surface from the wellbores. Since rock cuttings might not float well in low viscosity fluids, viscosifiers are needed to increase the viscosity of the drilling fluids. A common viscosifier example is clay. Some fluid loss control agents may also double as viscosifiers.
Surfactants
The use of surfactants is similar to that of emulsifiers and wetting agents. Surfactants reduce the interfacial tension between water and the surfaces it comes in contact with inside the wellbore, including oil, air, and solids.
Friction Reducers
Friction reducers help to reduce the high friction pressures that are generated from the rapid and powerful injection of drilling fluids into wellbores. There is so much more about this oilfield chemical. Our article on friction reducers tells you everything you need to know about them.
Shipping Bulk Drilling Fluids and Additives for Oilfields
These drilling fluids are very important in the oilfield, and oilfields cannot do without them. A drilling site has to have these chemicals ready for use because millions of dollars could be lost otherwise. And that is why oil producers often knit close partnerships with the oilfield chemical logistics companies.
Challenges of Shipping Liquid Bulk Fluids and Additives for Oil Fields
Every oil company wants one thing amongst many others: a comprehensive logistics and distribution management system that helps them optimize cost and reduce out-of-stock situations. But this is a major challenge for the oil companies, as achieving this aim is easier said than done. There are just so many parties involved in the coordination of these supply chains. For instance, a supply chain would need inventory supervisors, site foremen, purchasing directors, third-party freight managers, carriers, shipping warehouse managers, and that’s just naming a few.
Another challenge that confronts oil companies is the usually vast sizes of the oilfields, with some being hundreds of miles wide in size. This is a problem because oil and gas drilling has not evolved to a level of complete technological automation. Everything has to be done manually.
And operators carry out so much chemical monitoring manually, they have to rely on their field experience and tools that are prone to error from years of use. But with nothing but their experience and these inaccurate tools, operators have to monitor chemical stock levels, injection rates, chemical supply, and production rates. These responsibilities are hard to lay on the shoulders of experience alone, as production rates are often inconsistent and forecasting becomes difficult.
Without putting proper planning and a reliable oilfield chemical logistics company in place, the consequences would be dire. A timeout of a few hours on the part of the logistics company could lead is too much time to waste. That is why it is best to partner with an experienced and reliable oilfield chemical logistics company, such as Total Connection.
Shipping Your Oil Fields Drilling Fluids and Additives with Total Connection
Total connection offers you something many other logistics companies struggle with. One of them is experience. We aren’t just talking about general logistics experience. Anyone can offer you that. We’re talking about hardcore experience in shipping oilfield chemicals to drilling sites effectively, efficiently, and reliably on a routine basis. Total Connection has almost three decades of experience in that. And in that time, we have worked with budding oil companies to the largest oil production companies with sustained success.
From experience, we are already familiar with all the possible challenges that may befall your oil production company. And we have the skills and networks that foresee and minimize your risks because of these challenges. With these skills and networks, we have forked out significant opportunities that remain unknown to other logistics companies, to save you costs while minimizing the likelihood of out-of-stock situations.
Let us know how we can help tighten up your oilfield drilling fluid and additives supply chain. Start by filling out the quote form below. We’ll be glad to partner with you.