The paints and coatings you see on your walls and other painted surfaces around you aren’t just mere paints or coatings. They have had other chemicals in them that boost their inherent properties and/or provide them with new ones. We call these chemicals additives.
Paints and coatings are never without additives. And in this piece, you’ll learn:
- What paint and coating additives are
- The importance of additives in paints and coatings
- The types of coating and paint additives, and
- How to ship paint and coating additives
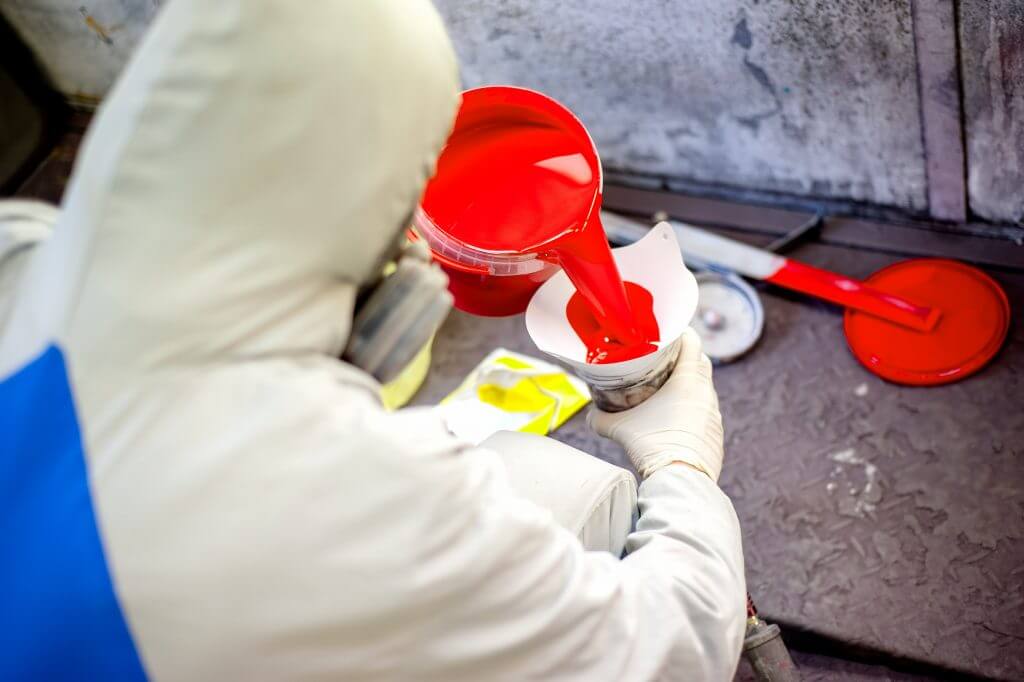
What Are Paint and Coating Additives?
We add additives to paints and coatings to make them suitable for specific applications by modifying or adding to their physical and chemical properties. There are over 20 paint additives, including wetting agents, coupling agents, and thickeners.
While non-industrial coatings might not have a lot of responsibilities beyond aesthetics, industrial coatings are often purpose-driven. And before a coating is chosen for an industrial application, it must possess characteristics that qualify it for such application. Most of the time, however, the coatings that come closest to meeting the requirements for their potential applications still end up lacking some crucial characteristics. But thanks to additives, we can optimize these paints and coatings to suit our desired applications and even more.
For instance, water-based corrosion inhibitors are additives that help marine coatings protect metals from corrosion. And thanks to the various coating additives, we have coatings that are more durable, algae resistant, rapid drying, or antifungal paints.
The Importance of Additives in Paints and Coatings
Here are some reasons additives in paints and coatings are so important:
● Stain Resistance
Stains on paints are one way a painted surface loses its attraction. And the reason some painted walls easily get stained is that the paints or coatings contain some microscopic pores that stain particles can fill up, making it hard for them to come off. However, some additives seal up the pores paints might have. This way, the stain particles have nowhere to hang on to, and they are easy to clean off.
● Leveling
The leveling of a coating is crucial to its longevity on the target surface. This is because the materials in coatings often have irregular shapes, and are liable to make the coated surface look rough after you apply them. This happens when the paint surface doesn’t flow well or dries too quickly. And it may also lead to the formation of bubbles or fish eyes on the surface.
A solution to this is the use of paint leveling additives to cause the coating to flow more smoothly and more slowly. This way, no surface is covered too thinly and the effects of uneven leveling are kept at bay.
● Hardness
The hardness of a paint or coating makes it resistant to scratches and marking. These kinds of coatings are mostly needed in areas of applications where the painted objects are prone to abuse. The addition of hardening additives to these paints makes them able to withstand the assault of abuse in these areas of application.
● Gloss
Depending on the application, manufacturers can make paints more or less glossy. They do this with the help of some paint and coating additives.
● Corrosion Resistance
Coatings to be used on surfaces that are at risk of corrosion often have corrosion inhibiting additives in them to protect their substrates. Some of these substrates include metals used to build marine products.
The reasons we use additives in coatings and paints are as many as the types of coating additives we have. And this brings us to the various types of coating additives:
Types of Coating Additives
The types of coating additives are numerous because there are just too many potential applications, but no perfect paint or coating that meets all requirements. And that is why we need just as many coating additives to help us enhance the properties of the coatings we have to suit specific applications. Here are some of the most common types of paint and coating additives we use in the industry:
1. Wetting and Dispersing Agents
A wetting agent is a surface-acting agent (surfactant) that reduces the surface tension of water so that its molecules are more adhesive. These additives are especially important in pigmented paints. Pigments are solids that have to first be dissolved in liquid phases of solvents and binders before application. When wetting agents are added to this mixture, it encourages the liquid phase to mix better with solid particles of the pigment, leading to a more stable and high-performance paint.
Dispersing agents are not so far away from wetting agents. In fact, they are both used in the same process. Only that dispersing agents help the particles of the pigment to remain scattered in the liquid phase without re-agglomerating.
Examples of wetting and dispersing agents used in paints include aromatic ethoxylates, polyether amines, aromatic ethoxylates, soya lecithin and derivatives, block copolymers, sulfonates, and many more.
2. Coupling Agent
Coupling agents encourage the adhesion within the materials of a paint or a coating through the formation of chemical bonds. This is usually within organic and inorganic material. A common example of a coupling agent used in paints is the silane coupling agent.
Adding a silane coupling agent to a primer causes silicon atoms to form covalent bonds that make the primer more stable and aid the dispersion of fillers. Coupling agents may also help make the coating more UV resistant.
3. Rheology Modifier
Rheology modifiers are also known as rheology control additives or thickeners. Their purpose is to regulate the rheological properties of the coating by making it more viscous. The higher the viscosity, the more likely it is for the coating to resist sagging due to gravity during application. Other uses of rheology modifiers in coatings are that they encourage leveling and make application easier.
Common examples of rheology modifiers in paints and coatings are Hydrophobically modified ethoxylated urethanes (HEUR), Hydrophobically modified alkali-swellable emulsions (HASE), cellulosics, fumed silicas, and organoclays.
4. Defoamer
As the name suggests, defoamers remove foams from paints and coatings immediately after their application. These foams are due to the incorporation of air into coating during its production, handling. While the bigger air bubbles are quick to escape, the very small ones can remain underneath the surface of the coating even after application. And if the air does not leave the coating, it causes bubble marks to show on the painted surface, leading to further defects down the line.
So, the defoamer has to bring the air bubbles to the surface where they get to escape. Examples of defoaming additives used in coatings include silicone-based defoamers, oil-based defoamers, and non-silicone defoamers.
5. Anti-settling Agent
Anti-settling agents have their application in water-based paints where the settling of components is likely to happen during storage or application. Three popular types of anti-settling agents used as additives in paints and coatings include polyolefin particles, fumed silica, and organic bentonite.
6. Anti-skinning agent
Paints are produced in bulk, and so storing them for long periods is unavoidable. However, when large quantities of coating remain in storage for a long time, they tend to form skins on the surface. This happens when the drying additive that should only take effect after application takes effect during storage. The downside to this is that skinning causes the coating film to dry and become harder to apply. But thanks to anti-skinning agents, we can store coatings for a long duration without skin formation. An example of skinning agents is methyl ethyl ketoxime.
7. Anti-sagging agent
The most common area of application of anti-sagging agents is in dense coatings. During and after application, these dense coatings are likely to sag in response to gravity, thereby leaving room for defects. Anti-sagging agents help to prevent this from happening.
8. Leveling agents
The surface of paints and coatings would bear brush marks, holes, and little craters during and after application. These lead to uneven leveling which leaves the door open for more defects later on. Leveling agents, however, seal the surface of the paint to make it look smooth and glossy.
In addition to that, thinner coatings can benefit from the use of leveling agents because they are most liable to retain marks during application. Examples of paint leveling agents are silicone-based leveling agents, fluorosurfactants, and polyacrylates.
9. Ultraviolet absorber
The effects of UV rays on coatings and paints are often detrimental. Ultimately, UV rays hurt the durability of the coating, and may even penetrate the surface to continue its degradation process. But the presence of UV absorbers in the coatings keeps UV degradation bay. UV absorbers absorb the UV rays incident on the coating and release them in the form of non-harmful heat. Apart from their use in coatings, UV absorbers are used as polymer additives.
10. Antistatic agents
Some coatings tend to accumulate static electrical charges that are capable of inducing electric shocks. While these electric shocks may not be dangerous to adults, the same cannot be said for kids. That is why we use antistatic agents, or conductivity agents, as additives in these coatings.
As the name suggests, antistatic agents prevent the coatings from accumulating electric charges. Aliphatic amines, ethylene glycols, quaternary ammonium salts, and phosphate esters are common examples of antistatic agents.
11. Anti-scratch agent
Scratching is an issue for paints and coatings long after they have been applied. Apart from ruining the attractive look of the painted surface, scratches can open up weak spaces for bigger issues like corrosion to attack. In the end, the coating loses its durability.
But with scratch and mar-resistant agents, the surfaces of the coatings are tougher against scratches. Examples of scratch and mar-resistant additives in paints and coatings are waxes, such as petroleum, natural, mineral hydrocarbon, and synthetic waxes. Other examples are polydimethylsiloxane (PDMS), colloidal silica, and aluminum oxides, and silicon oxides.
12. Matting agent
Matting gives a coated surface a clean and smooth finish with a minimum gloss. The reasons for using matt finishes are both aesthetic and functional. On the aesthetic side, the matting effect helps reduce glare by scattering the light rays incident on the coated surface. And on the functional end, the matting is a good way to hide imperfections on the surface of the coated substance. The additives that produce this matting effect in coatings are called matting agents. Examples are waxes, fillers, and silica.
13. Paint Preservatives
The majority of the paints we have now are water-based. This is an improvement from the solvent-containing paints that were around over 30 years ago, which had high harmful VOC emissions. The switch to water-based paints has helped with this, but it is not without its disadvantages. One of which is its proneness to microbial attacks that cause the paint to degrade. And that is why we use biocides as preservatives in paints; to keep them from spoiling even after long storage.
14. Anti-mold agent
Surfaces in humid areas are prone to the formation of mold. And mold not only destroys the look of the surface, but it also destroys the coating, leaving the surface prone to other issues. In addition, molds are health hazards.
Although one could manually clean up molds from surfaces before they get too much, coatings that have anti-mold agents or mold inhibitors in them do not need this. Anti-mold additives make it hard for molds to stick to, or grow on coated surfaces.
15. Flame retardant
Flame retardant additives in coatings help prevent ignition or slow the spread of fire. Coatings containing these additives are common in areas of application where there is high human traffic, such as an office building. The flame retardants in the coatings on the walls of an office building, for instance, force the fire to spread more sluggishly than it normally would, buying more time for the humans in the area to evacuate. Flame retardants are also used in polymers.
16. Corrosion Inhibiting Additives
Corrosion has always been a major challenge for metals and other substrates that can corrode, and this threat will continue to loom as long as there is oxygen in the air and water molecules around. Corrosion hugely impacts the durability of substrates and makes them unable to perform their purposes effectively. And this is why the use of corrosion inhibiting agents in coatings used in corrosion-prone environments is non-negotiable. Some of the most common components in most of the corrosion inhibitors we have around are zinc and sodium nitrite.
17. Driers and Catalysts
Without driers in paints and coatings, these chemicals would take months to dry up after application. Driers are, therefore, additives that speed up the drying rate of paints after application by speeding up the autoxidation process. Thanks to driers, we have paints that dry up within hours after application. And a common example is cobalt. Other examples include zinc, bismuth, calcium, zirconium, lithium, and manganese.
Paint and Coating Additives Shipping
Like other industrial chemicals, paint and coatings need to be shipped in bulk to ensure that the production process of paints goes smoothly and uninterrupted. And there is no better way to do this than to have experts who understand the best shipping methods and the challenges to expect during the process. Examples of such challenges include:
● The Hazardous Nature of Some Paint and Coating Additives
Many additives are toxic or hazardous, and extra precautions have to be taken when shipping them. These hazardous chemicals must only be handled by professionals who understand the extent of repercussions that the mishandling of such chemicals can bear on lives and properties. These professionals must also know how to handle the additives without risking any hazards.
● Bans and Regulations
As you might expect, the shipping of chemicals that can be as potentially dangerous when mishandled as coating additives is fraught with regulations and even bans. Some of these additives have been banned in the US, while some are only shipped under scrutiny from regulatory bodies. It takes an up-to-date expert to keep up with these regulations.
● Shipping Conditions
The shipping conditions of the additives may also pose a challenge for shippers who don’t have the right equipment for it. Although tankers are generally the best shipping vehicles, some tankers need to be customized for the shipping of specific chemicals. For instance, some additive chemicals prefer not to be too agitated, which could be hard to achieve during transit. As a result, only tankers that perfectly fit the volume of the chemical with little space for agitation are best for these chemicals.
Shipping Your Bulk Paint and Coating Additives in Bulk with Total Connection
Total Connection is a third-party logistics company that has been in the business of shipping industrial chemicals for almost three decades. In that time, we have built up an enviable amount of expertise and experience that makes us stand out among others.
Our services are flexible and effective, and efficient. We offer you solutions that are best for your needs and your budgets. And by filling out the quote form below, you can partner with us and take your paint and coating additives shipping to the next level.