The international maritime sphere poses a lot of stress even for some of the most seasoned professionals with the sheer number of processes and paperwork involved. In truth, every professional that engages in international shipping is exposed to the complexity that comes with the maritime sector. And while human errors cannot be eliminated, they could pose serious risks and problems when they eventually occur.
As a direct response to this, different countries have come up with new processes and regulations to curb the possibility of errors and, by extension, serious risks. These regulations achieve this by simplifying specific complex import and export procedures. In the United States, one such regulation is the Automated Manifest System.
What Is An Automated Manifest System
The Automated Manifest System (AMS) is an electronic communication system that offers U.S Customs and Border Protection relevant documents before cargo arrives. On the other hand, AMS filing is a document provided to the CBP that highlights all cargo imported into the country. Importers or agents are mandated to file this document 24 hours before the vessel leaves the port.
Initially, AMS was implemented in 2004 as a system responsible for tracking freight and minimizing the time required to import shipments into the United States. However, this system has been scaled up to incorporate freight inspection to ensure the safety of imports entering the country. The AMS affects all cargo regardless of the mode of transportation
How An AMS Works
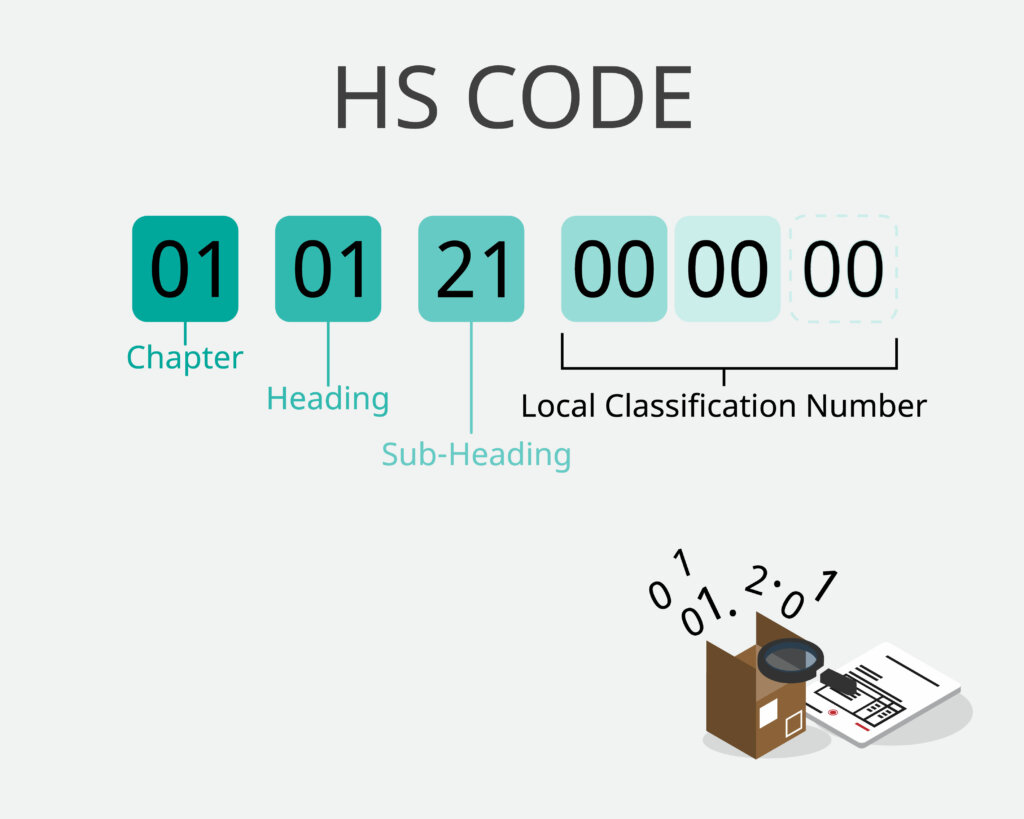
All importations into the US through air or ocean require some sort of declaration with comprehensive information regarding them. In line with this, customs officials utilize the AMS to disseminate electronic information and regulate cargo imported through sea, road, air, and rail.
Shipping lines, airlines, and other forms of freight transportation services are mandated to offer up-to-date cargo information within a particular timeframe, which is registered in the Automated Manifest System. The stipulated timeframe is 24 hours before the cargo leaves the port.
If for any reason, the cargo reaches the U.S without any record of it on the AMS, the cargo is sent back to the loading port with all costs placed on the exporter. Additionally, defaulting on the CBP’s requirements and deadlines attracts a fine of about $10,000 per violation.
Aside from the stipulated timeframe, other requirements include relevant information that must be correctly provided during the AMS filing. This information includes;
- Sender and recipient’s full names and addresses
- Carrier name, documentation country, voyage number, and standard carrier alpha code (SCAC).
- Details of the loading port
- Hazardous material code
- Details of cargo, including name, weight, and number.
- Last foreign port before cargo departs for the U.S
- Container identification number
- Container most recent seal number during cargo loading
- First foreign port of entry where carrier receives goods.
- Date of arrival in the U.S.
Often, AMS filing is straightforward; however, there could be complications in filing procedures if cargo is transloaded – transferring goods from one mode of transportation to another en route to their ultimate destination. In this case, AMS filing must be carried out at the last foreign port of transloading.
Registering For AMS Filing
AMS is filed by Non-Vessel Operating Common Carriers (NVOCCs) and freight forwarders at the export port. As such, these agencies are responsible for all inaccuracies in the information provided. The Automated Manifest System can be filed on the CBP website through the following steps.
- Select the “manifest(AMS)” menu and begin a new transaction
- Input all required information
- Select the “open AMS” tab and begin the AMS filing process.
- Enter all the relevant detail in the “AMS manifest” tab.
- Add the Bill of Lading on the “BOL tab.” This involves inputting details such as BOL number, foreign port of lading, SCAC code, city of origin, and the like.
- Add container information. For NVOCCs, select “NC” for non-containerized freight.
- Select the “Equipment Inventory” tab to enter any empty containers.
- Save and mark AMS filing as complete.
After completing the entire filing process, the manifest can be printed out and sent out from CBP’s website.
Benefits of AMS
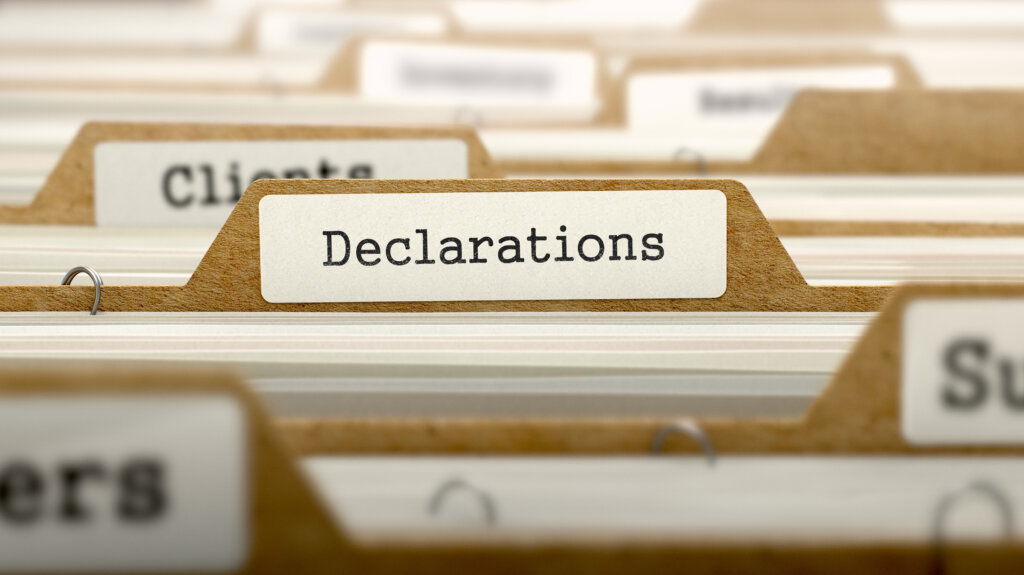
Following its implementation, AMS has been largely beneficial in the U.S maritime sector. Here are some benefits of the Automated Manifest System.
Convenience
AMS filing has vastly improved how convenient import and export processes are. It makes it easier for ports and the CBP to track and identify cargo before it enters the U.S. With all information on the shipping line, container, freight, and other online parties, it’s easy for the customs department to monitor all imports.
Efficiency
The electronic nature of the AMS has improved how efficiently shipping processes are carried out. Prior to the AMS, shipping and airlines were mandated to complete large volumes of documentation regarding the cargo and route. However, the AMS filing system has reduced paper-based documentation by accepting electronic data.
Clearance is now also done much faster with this automated system. Through accurate and fast data entry, the whole process is dynamized, thereby reducing downtime and possible overhead.
Security
Security was the initial factor that spurred the development of an automated manifest system. And while the system has been scaled to incorporate other features, security remains the most important. The CBP can utilize the AMS tracking system to quickly check the contents of cargo.
With cargo mandated to be registered, customs officials can now identify and deal with high-risk cargo that could potentially threaten the country.
AMS vs. ISF vs. ACE
All three are implemented to improve security in import and export processes. Yet, they all differ in one way or the other. Firstly, the automated manifest system filing specifies all imports into the U.S, including all relevant details. On the other hand, ISF needs a shipping agent, mostly the freight forwarder, to complete all shipping details of an import into the country.
The Automated Commercial Environment, or ACE, is a system utilized by different maritime professionals to register all imports and exports with the CBP. The ACE system ensures the accurate collection, processing, and exchange of data to the CBP, as well as other relevant federal agencies.
Let Total Connection Help You Stay Compliant with Your AMS Filings
AMS filing is reserved for shipping agents; to avoid unnecessary issues and delays with your import, you are better off engaging a quality third-party logistics service who is knowledgeable in the AMS process. In line with this, Total Connection provides quality, all-around service, which will include the monitoring of a timely AMS filing.
Engage us today by filling out the brief quote below.