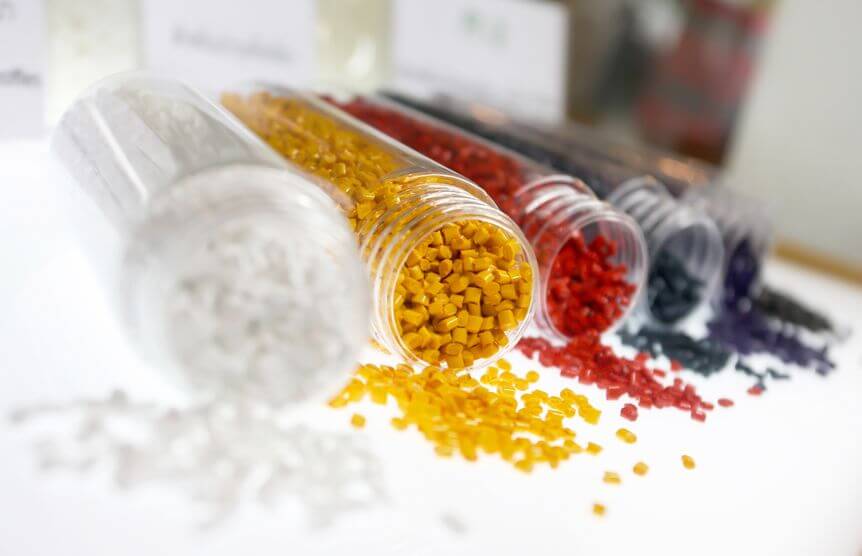
Plastic is one of the most abundant materials around us. We use it for everything, from furniture to electronics, automobiles, food packaging/containers, and many more. But what you might not know is that there are hardly any of these plastics without polymer additives in them. And the same goes for every other polymer.
When you consider how it’s almost impossible for us to completely do without plastics, you begin to understand the importance of polymer additives as well. So, this article is about the unsung heroes in the polymers we can’t do without — the additives in polymers.
This complete guide covers everything from what polymer additives are, their classifications, examples, FAQs about them, and finally, how to transport them in bulk.
What Are Polymer Additives
Polymer additives are chemicals we add to polymers to keep them from degrading, enhance their inherent properties, and/or give them new ones. Polymer additives are added to polymers to make them more easily processable, last longer, and/or meet specific requirements for a final product.
The Need for Polymer Additives in Plastics and other Polymers
Remember when we said how all plastics contain polymer additives, did you wonder why that is? Here’s one of the many reasons we need polymer additives in plastics:
Plastics, in their natural form, can’t stand heat and light without degrading. Expose them to either light or heat and see how quickly they degrade, discolor, and lose their durability. These processes are usually irreversible, so the only hope we have is to prevent them from ever even happening. And there are two ways to prevent this degradation from happening. The first is to modify the plastic itself or look for a replacement polymer. This method is, however, not economical because of the quantity of plastic we use. Modifying that much plastic would be very expensive. And getting a replacement polymer would mean searching for another polymer that is as abundant in nature as plastic and with similar properties. The options are very few.
The only other option is to enhance the stability of plastic to heat, light, or any other degradation factor with the use of polymer additives. This option is the best as it is effective and economical. You only need to add the additives to the polymers in very little quantities, but their effects are drastic and significant.
For instance, we use polypropylene in various applications, including convenience products, automobiles, and home appliances. But the flaw with ordinary polypropylene is that it cannot withstand high heat. Use it in an oven at 150℃ and watch it degrade within a day. But add as little as 0.4% antioxidant, and what used to degrade in 24 hours now remains undegraded, even after 2000 hours or more after exposure to heat. With that little antioxidant, we have been able to improve polypropylene’s resistance to heat without altering its inherent properties. Impressive, isn’t it?
Classifications of Polymer Additives
Polymer additives generally fall into two classifications. The first class of polymer additives is polymer stabilizers. You can also call them polymer property retention additives because they prevent the polymers from degrading and losing their properties.
But sometimes, merely stopping the polymers from degrading is not enough to prepare the base materials for consumer use. At these times, we add additives that offer more properties to the polymers. We call these other polymer additives functionalizing agents, and they make up the second classification of polymer additives.
As we go on, you may find that the line between the two classes isn’t so distinctive, as some additives may well fit into any of the two categories.
Polymer Stabilizer Additives
Polymer stabilizers help to prevent polymers from degrading during processing or consumer use. Some of the most common degradation processes that happen to polymers include thermal degradation, ozonolysis, oxidation, and the combinations of those. And when plastic or any other polymer degrades, you know by its change in color, appearance, and the diminishing in its strength and durability.
However, it is not enough to just pour just any kind of stabilizer into any kind of polymer. Instead, there are choosing processes depending on the polymer. The reason for this is that the factors that lead to degradation in polymers often vary. For instance, chlorine-containing polymers don’t degrade the same way as non-chlorine-containing polymers. It then makes sense to have different additives for either kind.
How Polymer Stabilizers Prevent Polymers From Degrading
To protect plastic from oxidative degradation, we have to hinder the radical reaction early in the degradation process before any destructive degrading happens. This involves abolishing every factor that could lead to degradation in plastic. And often, just one polymer stabilizer is not enough to do this job because one polymer can suffer from different degradation factors at the same time. That is why it is common to use more than one stabilizer type on a polymer to tackle whatever degradation factor the polymer may face.
For instance, phosphorus antioxidants and phenolic antioxidants are both used on polypropylene plastics to prevent thermal degradation and make the base material durable in different weathers.
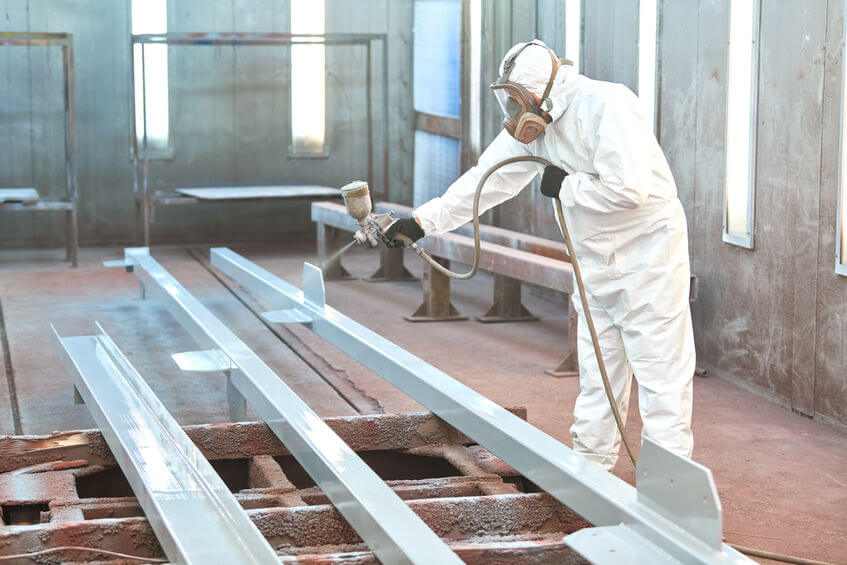
Common Examples of Polymer Stabilizer Additives
These are some of the most common polymer stabilizer examples there are:
- Antioxidants
When polymers react with the oxygen in the air, they tend to degrade in a process called autoxidation. Antioxidants combat this autoxidation process.
A good example of where antioxidants are put to work is in combating thermal oxidation in plastics. A lot of plastics are prone to degradation because of thermal oxidation, but their molding and casting processes involve the polymers being exposed to temperatures higher than their melting points. And at these temperatures, polymers react more rapidly with oxygen. And as a result, degradation of such plastic already starts from its processing stage.
But thanks to antioxidants, polymers can resist degradation long enough to make it past the processing stage and well into consumer usage.
- Light Stabilizers or Photo Stabilizers
The degradation process that light stabilizers inhibit is photo-oxidation, which is degradation caused by the combination of light and heat.
- UV Stabilizers
These prevent UV rays from degrading polymers through what we call the Photo-Fries rearrangement. Examples of polymers that are susceptible to UV degradation include polyurethanes, polycarbonates, and polyesters. So, what UV stabilizers do is that they absorb the energy from the UV rays and dissipate them as heat. Thereby, reducing the amount of UV the polymer itself absorbs, and ultimately slowing down the degradation process.
- Quenchers
There are other times the impurities in a polymer trap light, causing the polymer to get excited and full of energy. And when oxygen at room temperature gets into the mix, it’s converted to extra-reactive singlet oxygen. In simpler terms, this is just another recipe for degradation. But with the use of quenchers, we can absorb the extra energy from the excitation process and dissipate it as fluorescent light at a lower frequency or heat.
- Hindered Amine Light Stabilizers (HALS)
HALS are light stabilizers, but they also double as thermal stabilizers. As a result, the polymers they are added to have better weathering properties. Examples of such polymers are polyolefins, polyurethane, and polyethylene.
- Heat Stabilizers
Heat stabilizers are used to hinder the degradation of polymers that are prone to thermal degradation. A common example of such a polymer is PVC. In these polymers, the degradation process begins at temperatures above 70 °C, and it leads to dehydrochlorination or loss of HCl. Examples of heat stabilizers are metallic soaps and the derivatives of heavy metals, such as cadmium and lead.
- Acid Scavengers
Also known as antacids, acid scavengers help to neutralize the degrading effects of some acids, such as HCl, on the polymers. Apart from oxygen, light, and heat, acid impurities in polymers also lead to degradation. And besides reducing the thermal stability of polymers, these acid impurities may even corrode the polymer processing equipment.
- Aldehyde Scavengers
This is another class of scavengers, and their most common applications are in PET (for making water bottles), polyacetals, and formaldehyde-synthesized polymers. Bits of acetaldehyde form during the processing of these polymers, which can influence the taste of water in PET bottles. And to reduce the formation of this acetaldehyde, we introduce aldehyde scavengers to the polymer matrix.
- Biocides
Chemical reactions are not the only factors that lead to polymer degradation. Microorganisms can also degrade polymers. And to combat these microorganisms, we use bio-stabilizers, anti-microbials, and biocide polymer additives, such as isothiazolinones.
- Metal Deactivators
Metals can also be responsible for the degradation of polymers, especially in those polymers that come in contact with metal, like in electric cables. The metal ions that are often the culprits are aluminum, copper, and titanium. But we can add metal deactivators to the polymers that are susceptible to this form of degradation to improve their stability.
Functionalizing Agent Additives
Functionalizing agents are additives you add to polymers to either improve the inherent properties of the polymer or add to them. The ultimate aim of using functionalizing agent additives is to make polymers more suitable for a wider range of applications.
Functionalizing Agent Additives Examples
These are some of the widely used functionalizing agents there are:
- Plasticizers
Plasticizers are additives you add to polymers to improve their flexibility, softness, viscosity, plasticity, and friction levels. Plasticizers make it easier to handle the polymers during processing, while also getting them ready for consumer use. There are various kinds of plasticizers that possess properties that equip polymers for a vast number of applications, including construction, electrical cabling, fabrics, and medical products. Phthalate plasticizers are a common example of plasticizers, and they’re popular because of their useful applications in PVCs.
- Dyes and Pigments
Dyes and pigments are polymer additives that are used to change the colors of polymers.Dyes are preferred for transparent polymers despite their poor light and thermal stability. Pigments are often added to the polymers before the final products are molded, and they can be organic or inorganic.
Extra care has to be taken in choosing a colorant for a polymer because some pose health risks. For instance, synthetic dyes have to be flagged as safe by the right bodies before being used in consumer products.
- Flame Retardants
Flame retardant polymer additives are called into action in polymers that have the potential of catching fire when they’re exposed to high temperatures. Examples of where you would find such polymers are in electric devices and electric cables. And adding flame retardants to these polymers does the trick.
Flame retardants have three common ways of preventing combustion in polymers. The first is the use of chemical reactions to prevent combustion. The second is by forming a barrier between the surface of the plastic and combustion agents like heat and oxygen. Finally, some flame retardants decompose into water and evaporate when they’re exposed to heat, lowering the temperature of the polymer in the process.
However, different polymers have different preferences for flame retardants, and so careful considerations must be in place while choosing one.
- Anti-fogging Agents
Anti-fogging agent additives prevent water droplets from forming on the surfaces of the plastics. Polymers that need to retain their transparency are often the ones that use these additives. Some of the common areas of applications of anti-fogging agents are in greenhouse films and packaging films. And examples of anti-fogging agents include sorbitan esters, ethoxylated fatty alcohols, and glycerol esters.
- Antistatic Agents
It is possible for polymers, which are generally good insulators, to get electric. This happens when static electricity builds up in the polymers. And many polymers are susceptible to this, with only a handful being inherently antistatic. Common examples of antistatic polymer additives are polyethylene glycol esters, amines, and ammonium compounds.
In addition to stopping static electricity from forming on the surfaces of polymers, antistatic agents often double as electromagnetic shields.
- Nucleating Agents and Clarifying Agents
Some polymers specifically require these nucleating and clarifying agents. Crystalline polypropylene is an example of such a polymer. Adding a nucleating or clarifying agent to polypropylene boosts the mechanical properties of the polymer, making it more stable at temperatures that would have normally distorted it and giving it more transparency.
In addition to those, these functionalizing agents reduce the processing time of some polymers, cutting the production cost and increasing production efficiency. Examples of nucleating and clarifying agents include phosphate metal salts, metal carboxylates, and sorbitols.
- Lubricants
The use of lubricants as polymer additives is more popular during the processing of polymers. Lubricants lessen the friction between the particles of the polymers and the machines processing them. Without these lubricant additives, friction could make the plastics less moldable, resulting in rough finishes. But with them, production efficiency increases, and the appearance of the molded plastic is smooth and clean.
Common examples of lubricant polymer additives include fatty acid amides (oleic acid amide, stearic acid amide, erucic acid amide, etc), hydrocarbon lubricants. Metallic soaps, fatty acids and higher alcohols, and esters.
- Animal Repellents
Animals can also be a problem that requires the use of additives in polymers to solve. Have your pets ever gnawed at plastic materials that have no business being in their mouths? Or do those rats keep chewing up your electric cables and causing electrical problems for you? Adding animal repellent to the polymers you don’t want them getting close to solves this.
Animal repellent polymer additives are bitter (e.g. denatonium benzoate) or spicy (e.g. hot pepper) additives that pets, rodents, and other plastic-eating animals can’t stand. The strengths of some animal repellent additives could also be their unpleasant odors. While some make use of natural oils to repel birds.
- Blowing Agents
Blowing agents are used in foam making. These agents go through thermal decomposition during processing, release gases, and take up the foam structure we’re familiar with.
- Odor Maskers
Odor masking additives are pleasant smelling agents that are used to cover up the odor from degradation products or contaminants in polymers.
FAQs About Selecting Polymer Additives
Here are some of the frequently asked questions about the selection of polymer additives.
1. Why do polymers discolor?
Discoloration in polymers happens for various reasons. The common causes of discoloration of polymers are additives, impurities, the environment, processing conditions, and catalysts and promoters. A good way to avoid discoloration of polymers is to first consider the environment where the polymer would serve as a consumer product and its processing conditions. Considering these factors helps you to understand the potential interactions and reactions the polymer could have, and also to use the knowledge to come up with the best polymer additives for such polymers. A common example of a degradation-preventing polymer is an antioxidant.
2. How to avoid defective appearance in polymers
The common causes of defective appearances in polymers are dye-buildup, degradation, and extruded strands. For defects due to extruded strands, lubricant additives are best, since friction caused the strands in the first place. Removing insoluble compounds, adding compatibilizers, and fluorinated elastomers can often reduce dye buildup. And low molding temperatures help to ensure that the polymers are in not-too-high temperatures, thereby keeping degradation at bay.
But generally, using a phenolic antioxidant is usually a good way to prevent all kinds of appearance defects in polymers.
3. How to prevent polymers from degrading quickly when exposed to high temperatures?
Plastics are most guilty of degrading when put to use under consistently high temperatures. But this isn’t something a combination of phenolic and thioether antioxidants can’t solve. However, extra care should be taken when using thioether antioxidants because the chemical may release acids.
4. How do high temperatures affect plastics?
Thermo-oxidative degradation happens when plastics are exposed to high temperatures. In fact, the process speeds up when the plastic reaches high temperatures. Usually, the combination of HALS and thioether antioxidants is good enough to prevent thermo-oxidative degradation processes in plastics. But the downside is that this combination decreases the weatherability-improving property of HALS.
5. How to prevent degradation of plastics exposed to agricultural chemicals
Agricultural chemicals often tend to reduce the weatherability of plastics, as they have acidic substances in them. The curing catalysts in paints are also guilty of this. And in the case of greenhouse agriculture, these chemicals can even render the HALS in polyolefin incapable of providing effective weatherability. The best way to combat this is to use HALS that have low basicity, as these additives are reluctant to react with the acids.
6. What are bleeding and blooming in polymers?
Bleeding and blooming happen in polymers when the additives, especially plasticizers, float to the surface of the polymer as liquids or solids. Blooming refers to the solid discharge while bleeding refers to the liquid discharge. Both of them cause aesthetic defects to the polymers and they often happen when the polymer additives used are not compatible with the polymers themselves. Therefore, it is important to ensure that the additive choice for a polymer is compatible with it. Using additives that also suit the environments where the polymers would serve as consumer products.
7. What is fogging in polymers?
Fogging happens when additives in polymers volatilize from their polymers and stick to walls or glass while causing aesthetic defects in the polymer products. Additives with high molecular weight and low volatility are often great at preventing situations like this.
How to Ship Polymer Additives
Polymer additives are majorly industrial materials, and any shipping that concerns them is often in bulk. So, the best way to ship polymer additives in bulk is by land through tanker trucks.
And since many polymer additives are Hazardous Materials (HAZMAT), personnel handling the chemicals must go through appropriate and regular training. Because without regular training, it could be hard to keep up with the constant updates that regulatory bodies, such as the United States Department of Transportation (USDOT), make to the regulations that bind HAZMAT transport.
Keeping the chemicals in the right conditions during transit is also another important factor in the transport of polymer additives in bulk. The list of polymer additives we have is almost endless, with each of them having its peculiar properties. Some of these chemicals don’t do well under agitation, so only the right sizes of tanker trucks must carry them. Some other additives are very reactive and must never be transported with some other chemicals.
It is for these reasons and many more that you can’t afford to entrust your bulk polymer additives transport to incompetent hands. Your company could pay in expenses and reputation for it. What you need is the perfect mix of expertise and experience, and you’ll find them both in Total Connection Logistics Services.
Transporting Your Bulk Polymer Additives With Total Connection
Total Connection is a third-party logistics company that dedicates itself to the effective, efficient, and personalized servicing of your logistics needs. We ship all kinds of industrial chemicals, including polymer additives, and still ship some more.
In addition to our expertise and experience, we offer you something many other logistic companies can’t: flexibility. At Total Connection, we tailor our services to the specific needs of your company down to the littlest details. Our services are not so generic that some companies receive the short end of the stick. Instead, we satisfy your logistics needs in the best possible way that suits your business, its capacity, and its needs.
We already have hundreds of companies who can testify to the effectiveness and efficiency of our services. You can join them by filling out the brief quote form below to initiate the shipping of your polymer additives. Our experts will reach out to you shortly to discuss solutions for your logistics needs.