Shipping friction reducers are integral to the drilling and stimulation process an oilfield requires. The are part of a diverse oilfield chemicals ecosystem and necessary to operate a successful drilling or fracking operation. Friction reducers are one of the most important oilfield chemicals in this oil-drilling process. It would be next to impossible to conquer friction in wellbores without them.
This article helps you understand shipping friction reducers, what friction reducers are, why they are so important, and how to ship these chemicals.
What is a Friction Reducer?
During the drilling of oil reservoirs like shales or coal beds, massive volumes of water are pumped into the wellbores. And the rate at which this water is pumped leads to the generation of high friction pressures resulting from the turbulent flow of the fluid. This high friction pressure further leads to product losses. To combat this wastage, we use friction reducers.
Just as the name suggests, a friction reducer reduces the friction in wellbores while stimulation and drilling processes are ongoing in shales and coal beds.
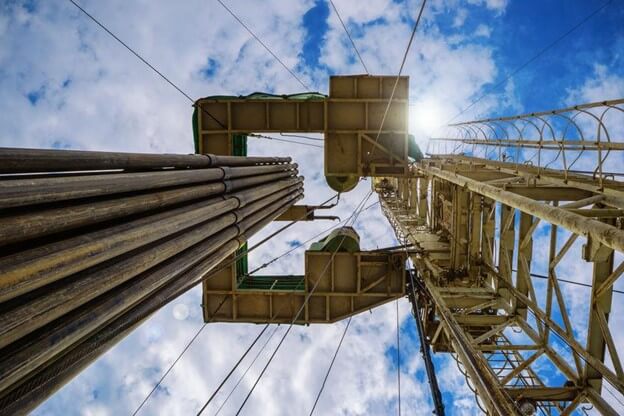
Any extraction process in environments with high levels of friction needs friction reducers to cut down on product losses and inefficient mining. That is why drilling sites are never short of friction reducers.
How Does a Friction Reducer Chemical Work?
Usually, friction reducers are made of a low concentration polyacrylamide polymer. During a process called fracking, the friction reducer is added to the base fracturing fluid to help keep the viscosity in the fluid close to the viscosity of water. This then significantly reduces the frictional effects of the fluid.
To better understand how a friction reducer chemical works and why it is so important, let’s elaborate more on its role in one of its most important usage scenarios; the fracking process
The Role of Shipping Friction Reducers in the Fracking Process
Fracking, or hydraulic fracturing, is a technique used for the recovery of oil and gas from shale rock. Miners drill wellbores miles into the earth before injecting water at high pressure (as fast as 100 barrels per minute) into the wellbores. This high-pressure water fractures the rock beneath and forces oil and gas out. But a side effect of this high-pressure water injection is a lot of turbulence and friction. And as it is with any system, friction leads to inefficiency and wastage of resources. Another disadvantage is the risk of damaging the surrounding areas, increasing the likelihood of fracking-induced earthquakes. That is why there is a need for a way to reduce the friction in the hydraulic fracturing system. The solution is in what we call slickwater fracking.
Slickwater fracking is simply the process of making the fracture fluid slick by mixing it with sand and other chemicals. This slickness reduces viscosity in the fluid, thereby cutting down on the friction significantly. And this is where the friction reducer comes in. In addition to scale inhibitors, biocides and surfactants, friction reducers are chemicals that help make up the slickwater. With the use of slickwater fracking, the risks of damaging areas surrounding the oil field are greatly reduced and there is a significantly lesser loss of products due to friction.
Types of Friction Reducers and What They are Made Of
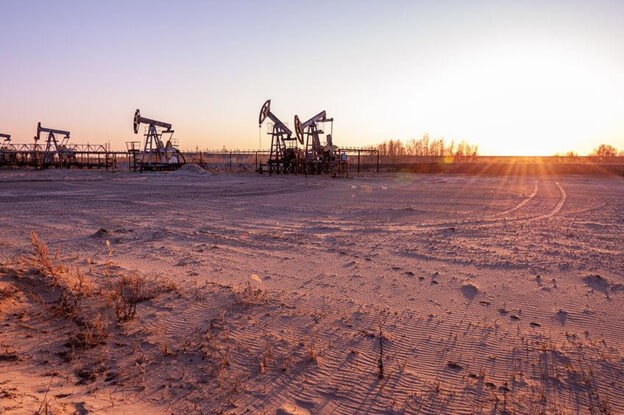
There are various types of friction reducer chemicals, depending on the purpose you need them from during the drilling and stimulation process. Some of them include gelling agents, while others don’t.
Acids
Production may be lower when you’re fracking at older wells than at newer wells. But a way to increase the production across the board, irrespective of how old the well is, is by acidizing the friction reducer. Acidizing the friction reducer clears up the damaged particles from drilling applications, leading to an enhanced production permeability.
Biocides
During the drilling process in an oilfield, some naturally occurring bacterial contaminations in hydrocarbons hinder production and render drilling inefficiency. This was a major oil drilling problem until the biocides were used to combat the bacterial contamination. Biocides control polymers that attract bacteria, iron-oxidizing bacteria, sulfate-reducing bacteria, and other bacteria that form slime.
Before you buy biocides, however, ensure that the company you are buying from offers only high-quality products. Low-quality biocides are now rampant, and they could cost you a lot on the oilfield.
Breakers
Breakers are a type of friction reducers that break crosslinkers and polymers in fracturing fluid, with the main purpose of lowering the viscosity of the fracturing fluid. Fracturing requires that the stimulation fluid be kept at a low viscosity after the application of a proppant. Breaker friction reducers make it hard for the proppants to return while making sure that only fluids return to the surface.
Buffers
Buffers help to manage the pH levels of the fracturing fluid to gain results that are stable and predictable from the process. The pH of the fracturing fluid affects some properties that are peculiar to the fluid, including break time, gelling agent hydration rate, and crosslink rate. Without a buffer friction reducing agent, these properties could result in an unstable result.
Examples of buffers include potassium carbonate, sodium bicarbonate, sodium hydroxide, and sodium acetate.
Other types of Friction Reducers
Those are not the only types of friction reducers that are used in oilfields. Others are corrosion inhibitors, clay stabilizers, and viscosifiers.
Shipping Friction Reducers via Liquid Bulk
The shipping of bulk liquid friction reducer chemicals is best done through the use of a stainless steel liquid bulk tanker. The reason is that stainless steel does not react with the friction reducer chemicals, thereby retaining the quality and content of the friction reducer.
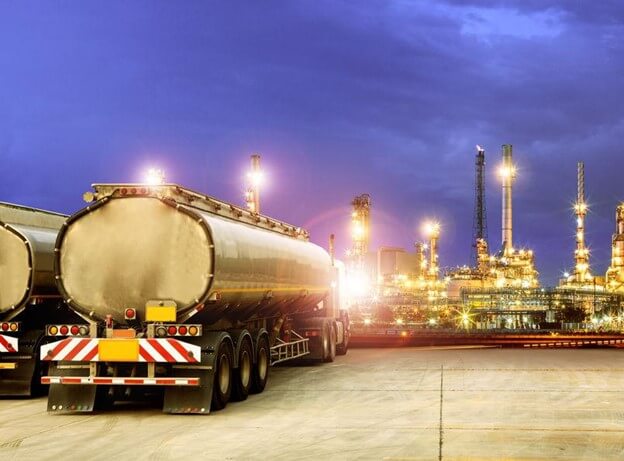
A lot of challenges may arise during the shipping of friction reducer chemicals, even though many of these chemicals are not hazardous materials. With the massive number of challenges that accompany the shipping friction reducers, it is important that you only entrust a reliable liquid chemical transportation partner, such as Total Connection Oil and Gas Logistics, to ship these chemicals.
Total Connection has the experience and knowledge of how to handle whatever tricky situations that may arise during the shipping friction reducer process. The company has a flexible yet disciplined delivery schedule that allows them to get your friction reducers to your oilfield as soon as you want them.
Conclusion
The importance of friction reducers in the oil and gas industry cannot be overemphasized. Without them, the drilling process could lead to the damage of the environment of the oilfield, water contamination, and other catastrophic consequences.
And just as important as the friction reducers are, so is the liquid bulk transport company that ships your friction reducer chemicals. When you partner with Total Connection, you would be making the entire process easy on your company and employees. You can start by filling out the brief quote form below.