Fire-safe plastics are crucial to our daily use. Without them, there would be a lot more fire outbreaks and higher fatality rates from these disasters than we have now. Because many plastics naturally tend to catch fire when exposed to high temperatures. Only polymers with inherent flame resistance can resist this tendency. Unfortunately, there aren’t many of them for the vast applications of polymers in our world. But the good news is that for these non-flame-resistant polymers, we have flame retardant polymer additives.
It isn’t enough, however, to just mix any kind of polymer with any kind of flame retardants and hope that the material doesn’t go up in flames. The processes of flame retardation in these polymers and the choice of the additives themselves are often complex. So, we have in this article everything you need to know about flame retardants, including:
- What flame retardants are.
- The need for flame retardants in polymers.
- How flame retardants work.
- Types of flame retardants in plastics.
- Different polymers and their compatible flame retardants.
- Flame retardants and their health concerns, and
- The best way to ship flame retardants.
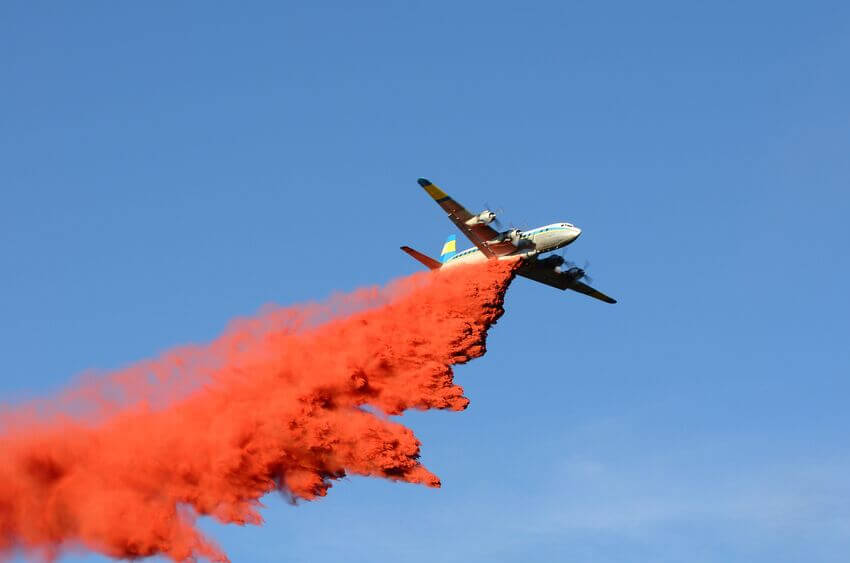
What are Flame Retardants?
Flame retardants are polymer additives that prevent ignition and/or retard burning in polymers using chemical and physical reactions.
You could try to make the polymer itself flame retardant by improving its intrinsic thermal stability. This would effectively make the polymers less likely to decompose from exposure to high temperatures. But it would be a more expensive venture, considering the volumes of polymers that would have to be intrinsically altered to meet up with the massive applications of the polymers. The cheaper, yet equally effective alternative is the use of flame retardants.
Flame retardants, like other polymer additives, only need to be added in negligible quantities. For instance, you only need between 2% and 10% w of red phosphorus flame retardant, depending on the polymer.
Additive and Reactive Flame Retardants
The additive flame retardant is the category of FRs that is physically mixed with the polymers during processing. Reactive FRs, on the other hand, have to mix with their polymer bases through chemical reactions.
Additive flame retardants don’t need to react chemically with the polymers, so manufacturers can mix them at any stage during the manufacturing process. While this is an enormous advantage for additive flame retardants over their reactive counterparts, the effect of the latter is usually more lasting than that of the former because they bond chemically with the polymer. But since reactive flame retardants must be added reactively to the polymers, this must be done in the early stages of polymer manufacture.
The Need for Flame Retardants in Polymers
There are many reasons we need flame retardants in polymers. Flame retardants:
- Inhibit fire outbreak or its propagation by increasing the flame retardant property of the polymer.
- Help to preserve lives and properties.
- Make the duties of fire service operators easier.
How flame Retardants Work
Flame retardants are different in their working mechanisms. A good starting place to understand how they work is knowing how polymers burn or ignite.
When exposed to heat, polymers emit combustible gasses. These gases mix with oxygen in the air to start ignition. And as long as the polymer has not completely decomposed, it gives off the gas that burns continuously, serving as fuel to the fire. The heat from the fire also returns to the system to keep the fire going. And it goes on and on until the polymer is completely burnt.
During the process, you might observe that the three most important factors are heat, fuel, and oxygen. And these three factors lead the polymer into various stages of the combustion process that comprise heating, decomposition, ignition, spreading of the flame, and smoking.
Without having all these factors to set up the combustion process, there’s no way burning could happen. And this is where our heroes come in. Flame retardants work by breaking the combustion process by removing any of the requisites for combustion.
There are three means through which flame retardants do this: Vapor Phase Inhibition, Solid Phase Char Formation, and Quench and Cool.
The Mechanisms for Flame Retardants In Polymers
Flame retardant retardants deter ignition and burning in the following ways:
1. Vapor Phase Inhibition
The vapor phase inhibition of flame retardants involves the disruption of the release of the flammable gases that polymers release when exposed to heat. Flame retardants disrupt this process by cooling the polymer so that there isn’t enough heat to cause the expulsion of the combustive gases. The desired consequence is that there isn’t enough gas to start the ignition or keep the burning going.
Although the choice of flame retardant depends on the polymer itself, the two most common compounds used for this kind of vapor phase inhibition are chlorinated organic compounds and brominated compounds. These compounds interfere with the gas phase by releasing chlorine or bromine ions that break the combustive gases reaction process in the polymers. The effect of this process on the flame is that it either slows or dies.
2. Solid Phase Char Formation
The solid phase char formation is a mechanism some flame retardants employ to break the combustion process through the formation of char. A flame retardant that has this property causes a layer of carbon (char) to form on the surface of the polymer This layer of char then serves as a barrier between the polymer and the heat from the environment.
Apart from forming a barrier, the solid-phase char formation flame retardant also doubles as a hindrance for the flammable gas in the polymer to escape. This ability comes in handy when there is eventually enough heat to force the release of the combustive gases despite the char formation. The char then hinders gases from getting out.
Common examples of flame retardants that fall into this category are melamine-based flame retardants. The molecular structure of these compounds changes into cross-linked structures when they are exposed to heat. And this is where the char comes from.
3. Quench and Cool
Quench and cool flame retardants make use of hydrated minerals to disrupt the combustion cycle. When these hydrated minerals are exposed to heat, they release the water molecules in them, which in turn cool the polymer and prevent the polymer from letting off its flammable gases.
The compounds that fall into the quench and cool category of flame retardants are magnesium and aluminum compounds. Besides releasing the polymer-cooling water molecules, the retardants also starve the polymer of the energy it requires to sustain burning. Another positive consequence is that this process forms a layer of char that further protects the polymer.
Classifications of Flame Retardants Used in Polymers
Flame retardants exist in several classes. And each class has peculiar properties that make it suitable for specific applications. The six most common of these flame retardant classes are:
- Halogenated flame retardants
- Phosphorus-based flame retardants
- Melamine flame retardants
- Phosphate flame retardants
- Metal hydroxide flame retardants
- Silicon-based flame retardants
But of these six, we’ll only discuss the first three:
1. Halogenated Flame Retardants
The two halogenated flame retardants we use in polymers are the brominated compounds and chlorinated compounds. Fluorides don’t make it to the list because of their low effectiveness. Iodides also fall short because of their thermal instability at the temperature ranges where polymers are processed.
a. Chlorinated flame retardants
Chlorinated flame retardants (CFRs) contain chlorine in high concentrations, and they are mostly used in the vapor phase inhibition of flames. They aren’t deployed alone into the polymers, however. Synergists (such as antimony trioxide) are used in combination with them. Chlorinated flame retardants often fall into two categories: chlorinated paraffin and chlorinated alkyl phosphate.
Depending on how long the paraffin chain is, chlorinated paraffin flame retardants are either liquid or solid. And their most common application is in combination with DP or DOP as a plasticizer for flexible PVC. Cables and flooring materials built with this flexible PVC have flame retardant properties. Solid chlorinated paraffin is also useful in combination with a synergist in thermoplastics. Chlorinated alkyl phosphate flame retardants, on the other hand, are used in flexible and rigid polyurethane foams.
Before you choose any chlorinated flame retardant to use in your polymers, consider its chlorine content, physical form, volatility, and thermal stability. Common examples of CFRs are bis(hexachlorocyclopentadiene)cyclooctane (dechlorane plus), hexachlorocyclopentadienyl-dibromocyclooctane (HCDBCO), and tris(2-chloroethyl)phosphate (TCEP).
b. Brominated flame retardants
Brominated flame retards make up the largest volume of flame retardants used in the polymer industry today. This popularity is because of the versatility of the group. Brominated flame retardants are easily processable, affordable, possess high flame retardant properties, and impressive chemical properties.
Using brominated flame retardants in combination with minerals also increases the mechanical properties of the polymers they are added to, while reducing the corrosivity and opacity of the fumes released as they burn. These properties make the fire retardant perfect in buying time for the escape of people who are caught in a fire outbreak. The environmental benefit is that there is less emission of toxic fumes into the atmosphere.
Selecting a brominated flame retardant is not as straightforward. There are many factors to put into consideration. Some of these factors include the cost, processing characteristics, type and content of the bromine in the compound, aging characteristics, and UV stability. Other factors include the standards that must be met and the environment.
Being as popular as they are, brominated flame retardants are useful in various applications, such as textiles, construction, furnishing, wire and cable, connectors, printed wiring boards, electronic enclosures, and many more.
Some of the most common examples of brominated flame retardants are polybrominated diphenyl ethers (PBDE), hexabromocyclododecane (HBCD), and tetrabromobisphenol A (TBBPA).
2. Phosphorus-based flame retardants
The two common phosphorus-based flame retardants used in polymers are red phosphorus flame retardants and organophosphorus flame retardants.
a. Red phosphorus flame retardants
You’ll often find red phosphorus (P-red) flame retardants in thermoplastics (polyesters, polyamides, etc), natural fibers (cotton and cellulose), and thermosets (epoxies, polyisocyanates, etc). But its use is limited by color to only gray and black materials.
Ironically, red-phosphorus is an ingredient on the striking surfaces of matches, yet when added in negligible quantities to polymers, retards the propagation of fire. Its flame retardation mechanism is solid-phase char formation.
One of the best things about red phosphorus flame retardants is that they are mostly used to meet high flammability demands. Polymers that have P-red flame retardants in them can withstand up to 320 degrees without decomposing, corroding extrusion equipment, giving off toxic substances, or releasing carbonaceous substances. In addition, they possess remarkable mechanical and electrical purposes.
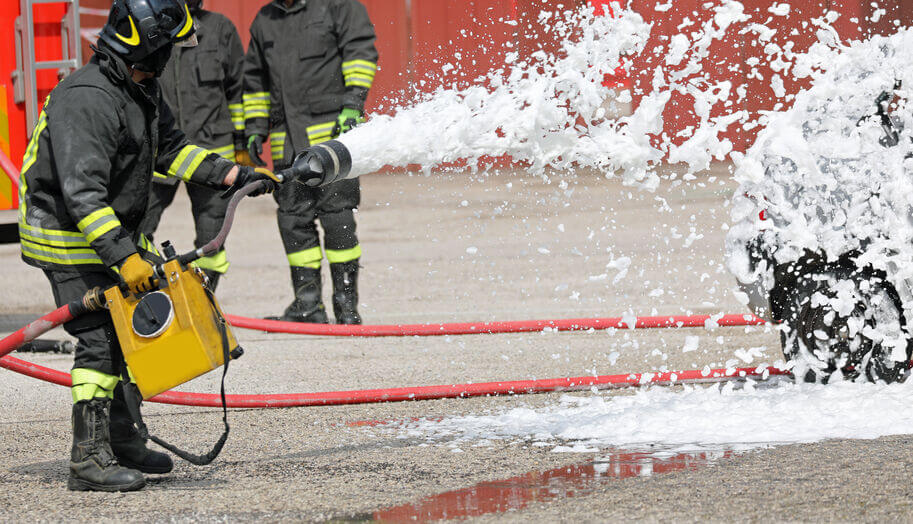
b. Organophosphorus flame retardants
The manufacture of thermoplastics alloys is one of the most popular areas of application of organophosphorus flame retardants. PC-ABS and PPO/HIPS are thermoplastic alloys that require specific flame retardant requirements, like the UL94 V0. One of the flame retardants that help these thermoplastic alloys reach these standards is organic phosphorus flame retardants. And in addition, they often impress UV stability on the resin.
Another common space where these flame retardants are used is in the production of polyurethane foams. Apart from their flame retardance, these phosphorus-based flame retardants are used in this application because of their easy processability and impressive physical properties.
There are many other areas of applications of organophosphorus flame retardants. But like every other flame retardant, thoughtful consideration has to be invested into choosing a polymer to use them with. One factor to consider is migration because phosphorus-based flame retardants are likely to migrate out of their base materials after some time. Foam density is another enormous factor when the compound is to be used in flexible PUR foams. Other factors include scorching, viscosity, and fogging.
Examples of organophosphorus flame retardants are tris(2-butoxyethyl) phosphate (TBOEP), tripentyl phosphate (TPP), tris(2,3-dibromopropyl) phosphate (TDB99), phenyl propan-2-yl hydrogen phosphate (PPHP), and many more.
3. Melamine Flame Retardants
Melamine flame retardants (MFRs) are a class of non-halogenated flame retardants that break the combustion cycle in polymers through the formation of solid-phase chars. The common subclasses in this class include melamine derivatives (organic or inorganic acids with salts), melamine homologs (such as melem, melon, and melam), and pure melamine itself.
These compounds of melamine may not yet be as popular as the other classes of flame retardants, but they are quickly growing in popularity. And their recent spurt in growth is because of their outstanding performances when it comes to affordability, safe handling, low corrosion, toxicity, and smoke density levels, and their general eco-friendliness. Another reason is the compounds’ ability to retard flame through several mechanisms.
The areas of application of melamine-based flame retardants are polyamides, flexible polyurethane foams, thermoplastic polyurethanes, and intumescent coatings. An example of MFRs is melamine polyphosphate (MPP).
Different Polymers and Their Compatible Flame Retardants
For the various polymers that there are, there are some flame retardants that are most compatible with them. These FRs are often the most widely used and most recommended by manufacturers for use on these polymers. Here are 11 common polymers and their compatible flame retardants:
1. Acrylonitrile Butadiene Styrene
Acrylonitrile butadiene styrene (ABS) is a polymer best known for its high heat stability, toughness, and easy processability. Besides these, it also has remarkable chemical resistance and impact strength. The flame retardants most compatible with ABS are brominated flame retardants. However, the choice of the particular brominated retardant depends on the application.
2. High Impact Polystyrene
High-impact Polystyrene (HIPS) polymer has a combination of many remarkable properties that make it suitable for various applications. To keep up with its wide applications, a flame retardant that is also suitable for various applications must be used. That is one reason why brominated flame retardants are commonly used in combination with HIPS. Phosphorus flame retardants are, however, the more suitable option for the PPO-HIPS polymer.
3. Natural and Synthetic Rubbers
We use both natural and synthetic rubbers to make materials like seals, conveyor belts, protective coverings, medical products, etc. And the most compatible flame retardants for these polymers are cross-linked elastomers which make use of aluminum trihydroxide or magnesium dihydroxide.
4. Polyamide
Polyamide is most commonly used in carpets, textiles, and other areas of applications where its flexibility and strength are needed. Examples of these applications include guitar picks, fishing lines, medical implants, and many more. And for this polymer, magnesium dihydroxide flame retardant is preferred.
5. Polybutylene Terephthalate
Polybutylene Terephthalate (PBT) finds its purpose in many household items, such as irons and showerheads. They are also useful in vehicles as plug connectors. Although brominated flame retardants are the best for PBT, careful consideration should be taken to choose one that best suits the purpose.
6. Polycarbonates
Polycarbonate (PC) has its most common areas of applications in mobile phones, connectors, battery boxes, electrical chargers, and many more. Its toughness, strength, and resistance to high and low temperatures make it suitable for those uses. And after a series of trials, silicon-based flame retardants have been found to be remarkably compatible with PCs.
7. Polyethylene
Products such as trash bags, grocery bags, squeeze bottles, housewares, and packaging film all depend heavily on polyethylene (PE). PE, in turn, depends on magnesium dihydroxide and aluminum trihydroxide for its flame retardance.
8. Polyesters
The major area of application of polyester is in the textile industry because it doesn’t wrinkle easily and can also retain its shape after distortion. These properties make it a perfect fit for the clothes that we wear and many other fabrics. And the most commonly used chemicals for inhibiting ignition or burning in polyesters are brominated flame retardants.
9. Polypropylene
The use of polypropylene cuts across various areas and industries. It has applications in textiles, plastics, packaging, healthcare, automotive, and many more. And magnesium dihydroxide has proven to be one of the most compatible flame retardants with this polymer over time.
10. Polyurethane foams
Apart from seat cushions, polyurethane is also used in bushings for automotive suspensions, carpet underlays, gaskets, and many more. And for these polymers, brominated and phosphorus fire retardants are most compatible. However, the choice of the FR must be tested under the weight of careful considerations because of the high impact these FRs can have on polyurethane foams.
11. Polyvinyl Chloride
Polyvinyl Chloride (PVC) is probably the most commonly used of all these polymers, with areas of applications in many industries. Name an industry, be it electronics and electrical, automotive, healthcare, or housing and construction. There is a prime chance that PVC is used there. On its own, PVC could be pretty useless. But mix it up with some plasticizers, and you have one of the most widely used polymers in the world. The flame retardant that goes well with this widely used polymer is either aluminum trihydroxide or magnesium dihydroxide.
Flame Retardant Health Concerns
Some of the most common health concerns associated with flame retardants include adverse effects in both animals and humans, such as reproductive toxicity, disruptions to the immune system, cancer, and neurologic functions.
The most vulnerable set of people to the adverse effects of flame retardants are children. Their organs are just developing, and not yet fully equipped to handle the potential hazards that flame retardants expose them to. And the most common culprits among flame retardants that are often responsible for these health risks are brominated flame retardants.
How to Reduce Exposure to Flame Retardants
There are a lot of ways to get exposed to flame retardants. It could be at your workplace, in your diet, vehicle, home, or anywhere else. There isn’t much you could do about coming in contact with flame retardants. But you are not completely helpless against these fire-retarding chemicals. Here are some things you could do to reduce exposure to flame retardants:
- When you need to purchase new products, go for those that are baby-friendly, as they often contain negligible traces of toxic chemicals.
- Go for furniture made from cotton, wool, or polyester instead of polyurethane foams.
- The surrounding dust could carry traces of these chemicals. So, provide good ventilation systems in all the rooms you’ll be spending a lot of time in.
- Washing your hands is highly underrated. But this simple practice can save you a lot of doctors’ appointments down the line. Always wash your hands.
To help you stay ahead of the game concerning the health hazards of flame retardants and to keep you safe from any other potentially toxic chemicals, use these government platforms:
- Centers for Disease Control and Prevention
- Consumer Product Safety Commission
- National Toxicology Program
- U.S. Environmental Protection Agency
Here is an example of Flame Retardents being demonstrated in a controlled environment
Video credit to: Commercial Products USA
Shipping Bulk Flame Retardants With Total Connection
What makes bulk flame retardants tricky to transport is that many of the chemicals are regarded as hazardous materials (HAZMAT). And because of this hazardous nature, a lot of care, planning, and consideration has to be put into the transporting of these materials. And with the ever-vigilant eyes of strict regulatory bodies (such as the United States Department of Transportation) monitoring your bulk flame retardant shipping, there’s no space for a misstep.
For this reason, leave the shipping of your bulk flame retardants in the hands of only the experienced and competent. And this is exactly what you’ll get with Total Connection logistics services.
Total Connection helps you handle your bulk flame retardant transport from loading down to offloading. You give the order, and you get your order as soon as you want it and where you want it. It’s that simple!
Your company too can enjoy an efficient supply chain, affordable shipping, and tailor-made services that the clients of Total Connection logistics company enjoy when you fill out the brief quote form below.