What is Formaldehyde?
Formaldehyde is a colorless and pungent-smelling chemical that is popular for having various forms which are all useful in a wide range of applications. Its most common form is formalin, which is simply formaldehyde dissolved in water. This versatile chemical is used to make other materials, such as plywood, adhesives and glues, and coatings. In addition, formaldehyde is also an important component in the making of some other chemicals.
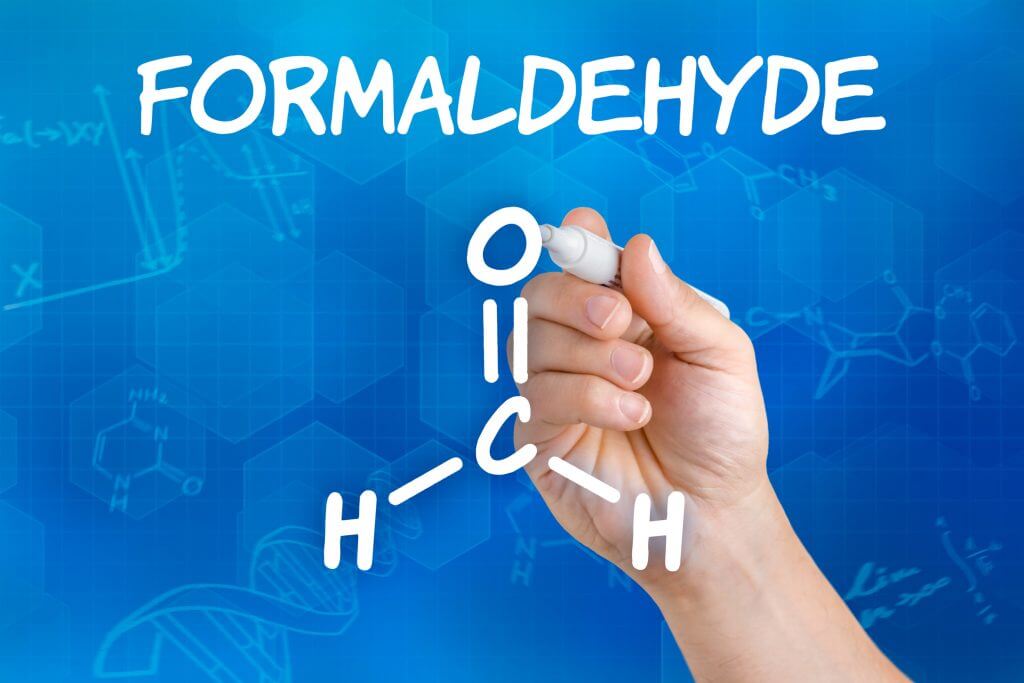
Production of Formaldehyde
Formaldehyde is a naturally occurring chemical in the environment. Most of it is produced in the upper atmosphere. The smokes from tobacco and forest fires also contribute to the formaldehyde content of the environment. Even you, I, and many other living organisms produce little amounts of the compound during our metabolic processes. In the laboratory, we produce formaldehyde through the oxidation of methanol.
Despite its wide range of applications, the use of formaldehyde is discouraged, limited, or heavily regulated because of its volatility, toxicity, and the health risk it poses to us.
Fortunately, this chemical doesn’t just accumulate in the atmosphere, as sunlight breaks it down within hours. It also doesn’t accumulate in soil or water, thanks to the bacteria that break it down here too. Another place formaldehyde could hide is in humans, but our body also breaks it down into formic acid so the toxic chemical doesn’t harm us.
Uses of Formaldehyde
- One of the most common uses of formaldehyde is in the making of resins. Some of the resins that have their origins in formaldehyde include melamine resin, urea-formaldehyde resins, methylene diphenyl diisocyanate, polyoxymethylene plastics, and 1,4-butanediol.
- Paints and explosives have pentaerythritol, which is a polyfunctional alcohol, in common. And formaldehyde is an important compound in the production of such alcohols.
- The textile industry induces crease resistance to their fabrics by using finishers made from formaldehyde-based resins.
- Formaldehyde is also used in the making of adhesives that are used in carpeting and plywood. But the chemical has to first be treated with melamine, phenol, or urea.
- Formaldehyde also finds use in pharmaceuticals. It is used to deactivate viruses used in vaccines. It is also used to make hard-gel capsules and anti-infective drugs.
Common Forms of Formaldehyde and Their Uses
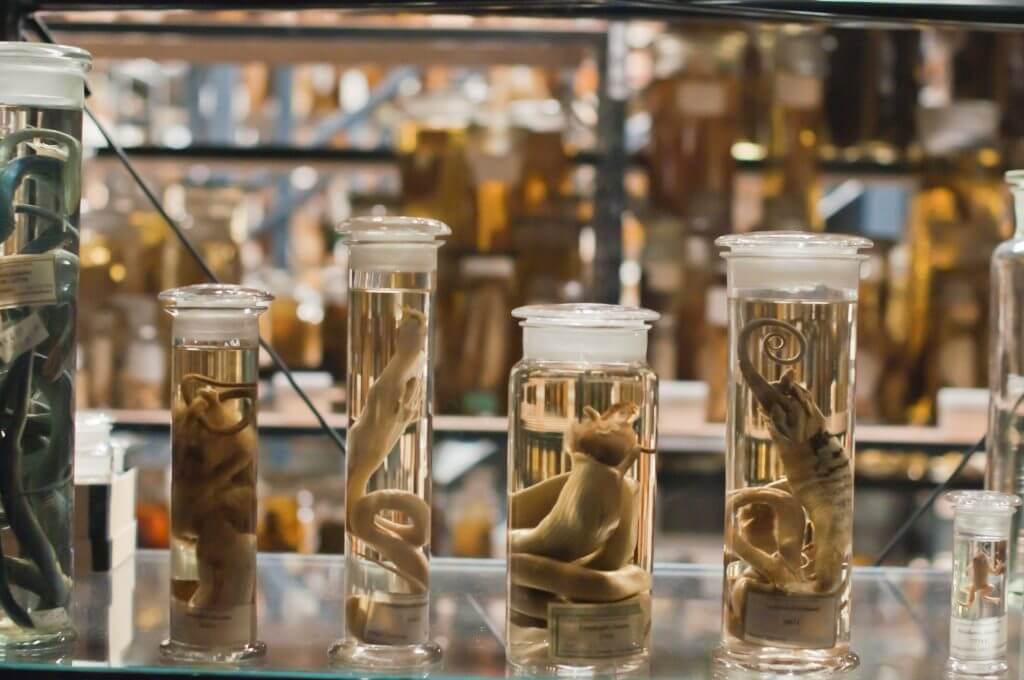
When you check the ingredients list of some products and don’t find formaldehyde, don’t be quick to assume that the product doesn’t have formaldehyde. Formaldehyde exists in many forms, and each form is useful for specific purposes. Some of the most common forms of formaldehyde are:
1. Formalin
Formalin is aqueous formaldehyde that is produced by simply dissolving formaldehyde in water until the perfect concentration is reached. Like formaldehyde, formalin remains colorless and retains its pungent smell. However, this solution tends to form molecular clumps that could force the formaldehyde to precipitate out of the solution. But methanol is added to the solution to prevent this from happening.
Uses of Formalin
- Formalin is a useful chemical in germicides and disinfectants. When formalin comes in contact with bacteria, parasites, and other potentially harmful microorganisms, it dehydrates and deactivates their proteins. This kills their cells, rendering the microorganisms powerless. However, formalin used around humans and any other organism you don’t intend to kill should be in dilute forms.
- Formalin is also used as a preservative in the storage of organ specimens and storage animals. The solution is also present in embalming agents and vaccines.
- Wart treatment is another area of application of formalin, but in very dilute forms. The formaldehyde solution breaks down the skin cells in the wart and could even kill the virus causing the wart. This use should not be self-prescribed, however, as it could invoke some allergic reactions in the user.
2. Paraformaldehyde
Paraformaldehyde is formed when formaldehyde polymerizes in water and precipitates out of the solution. In this form, it is a white precipitate with a slightly pungent odor. To stop the polymerization process from going too fast, methanol is added to the solution to stabilize it.
Uses
- A depolymerized paraformaldehyde forms a kind of formaldehyde that is very effective in disinfectant, fumigant, fixative, and fungicide products.
- Paraformaldehyde is also useful in identifying certain proteins and the DNA parts they bind to. This application is found in chromatin immunoprecipitation.
- Paraformaldehyde also serves as an alternative to aqueous formaldehyde in the production of binding materials made from resin. The end products are often plywood, particleboard, and fiberboard.
Shipping Formaldehyde and Formalin Products
With the wide use of formaldehyde, formalin, and their other forms, it only makes sense to ship them in bulk. But because of the hazardous nature of formaldehyde, you would be taking a huge and unnecessary risk when you ship it with the wrong logistics company. Apart from the health hazards it exposes humans to, the other disadvantages of mismanaging the shipping of bulk formaldehyde are:
- A drop in your product quality. And if you don’t discover this on time, it could cause a ripple of adverse effects on your company. First, you would be using substandard compounds, which would, in turn, make your products substandard. And this is in the best-case scenario. At worst, your freight would be completely useless, leading to loss of production time and other delays that could have been avoided.
However, this is a risk you don’t have to take when you ship your bulk formaldehyde and other related products with Total Connection.
At Total connection, we handle the bulk shipping of all kinds of bulk chemicals with maximum efficiency and effectiveness. We operate round the clock to make sure that your production process is never interrupted. Our customer service is also available every second of the day to get you whatever bulk shipping needs you may have.
You can be a part of our clients when you fill out the brief quote form. Then you can bid farewell to defective shipping for as long as your business operates.