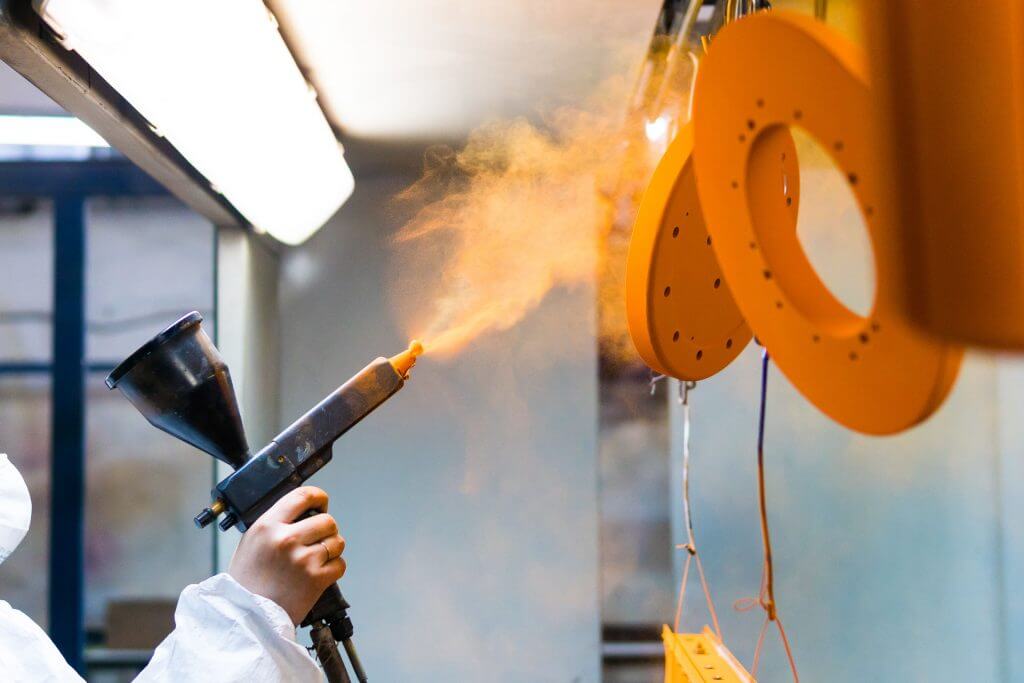
Look around you. You’ll find metals all around you. And every piece of it has been coated with a protective coating. There is hardly any construction work, especially those that involve the use of metals like steel and iron, that does not require the use of protective coatings.
Studies forecast that the protective coatings market would be worth $52.31 billion, thanks to its broad applications across industries, such as oil and gas, marine, automotive, construction, aerospace, power generation, and more. As a result, the protective coatings market is not only a huge one, it is also one we can’t do without.
What then makes protective coatings so important? Why can’t we do without them? And how does it affect you, the consumer? The best way to show you the importance of these chemicals is to make you see what they are used for.
What are Protective Coatings Used For?
These are some of the most common uses of protective coatings:
1. Corrosion Prevention
One of the biggest threats to the lifespan of metals is corrosion. What makes it worse is that corrosion doesn’t just start and end in a day. It happens over time, degrading the metal, and causing it to fail when you least expect it. And when the metal fails, the effects could be catastrophic, depending on where the metals are used. Therefore, we have to protect the metals from corroding, so we can extend the lifespans.
Protective coatings prevent corrosion in three major ways: inhibition, sacrificially, and through barrier formation. Some types of coatings merely serve as a barrier to protect the substrate from corrosive electrolytes. Other protective coatings serve as inhibitors to the formation of the electrolytes that lead to corrosion, preventing corrosion even before it begins.
Another way protective coatings, such as zinc-rich coatings, go about this is sacrificially. That is, they corrode in place of the metal substrate. And as the coating corrodes, it forms a protective barrier over the application surface to further protect it.
2. Chemical Protection
Some surfaces get to come in contact with chemicals during their lifetime. For instance, the walls of a chemical factory need protection, and so does the interior lining of tanks that carry chemicals. Otherwise, the chemicals could destroy these surfaces. And this is where protective coatings wade in to save the day.
Some protective coatings have chemical protection properties that protect the surfaces they are applied on from being damaged by chemicals around.
3. Weather Protection
The weather can be one of the biggest issues of structures that are exposed to it. The reason for this is that it is unpredictable, persistent, and unforgiving. As a result, the weather could easily wear some surfaces out over time, and make them lose their integrity.
An example of the damaging effects of the weather on structures is when steel is exposed to heat, water, and oxygen from the atmosphere. What we have is the recipe for corrosion. Another example is the damaging effects of UV rays on exposed wood structures, causing them to crack, warp, and slough off.
But with the right protective coatings, we can reinforce our structures against the weather.
4. Hygiene
This is another important use of protective coatings. Some coatings won’t bow to influence from the microorganisms in the environment. Such coatings are often used in hospitals and laboratories to discourage the growth of bacteria and other organisms, such as mold and mildew. As a result, the rooms where they are used see lesser exposure to contamination by these microorganisms.
5. Fire Resistance
Uncontrolled fire leaves a devastating effect on the surfaces that it is unleashed upon, including hard surfaces like steel and concrete.
Fortunately, there are protective coatings that have fire-retardant properties. When you coat the substrate with these fire-retardant coatings, you make its surface impervious to the damage fire can cause to it. These fire-retardant coatings also slow the spread of fire, thereby protecting other surfaces around.
Examples of where we would need fire-retardant coatings are in fire-rescue vehicles, combustible materials like wood and fabric, and in airplane interiors.
6. Aesthetics
Although protective coatings are mainly for protection, as you may have guessed from the name, they can also be great aesthetic additions to structures. They bring color and life to the surfaces they are applied to.
In Summary
It is easy to see a painted structure and quickly assume that the painting is just for beautification. While this may be true, protective coatings do far much more than beautification. Protective coatings offer protection against the weather, chemicals, corrosion, fire, and other forces that attempt to damage our structures. And this is why they are so important.
But one thing that is just as important as the protective coatings is the way you ship them. Some protective coatings contain fumes that don’t bear good news when they are ingested. That’s why it is important to only rely on experts when shipping protective coatings in bulk.
At Total Connection logistics company, we seamlessly provide efficiency, affordability, and flexibility when it comes to the bulk shipping of just about anything. Find out how we can help you handle your shipping as well when you fill out the quote form below.